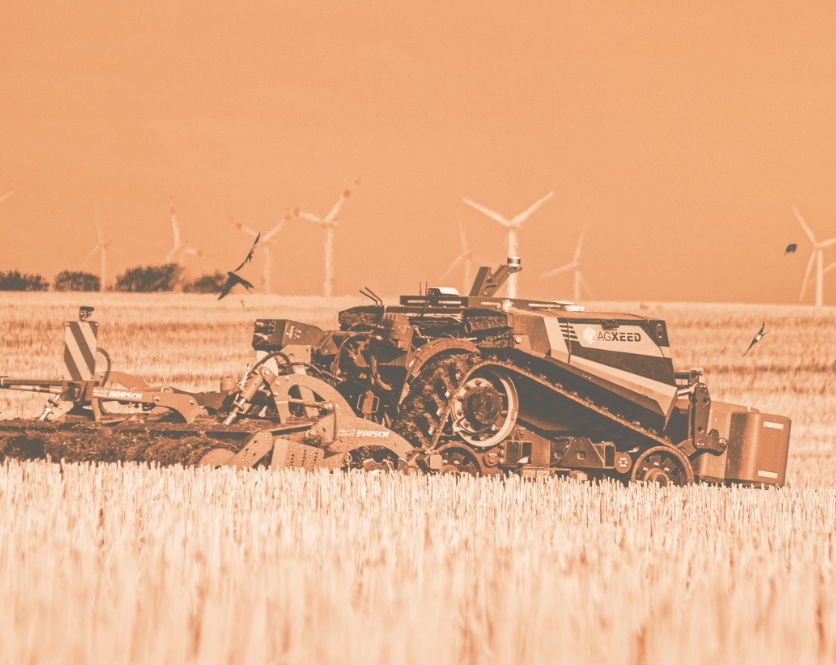
Robots in the Field
The world of robotics is advancing in leaps and bounds everywhere – including agriculture.
Read more
Tearing down the old production hall and building a new one. Assembling combine harvesters right up to the last day, digitalizing production, and realigning intralogistics: The “SynPro 2020” project stands for forward-looking modernization at the heart of the company’s headquarters. Time to visit the protagonists behind a project that poses a unique challenge – even for an established business like CLAAS.
Text: André Boße
“When the diggers come, that’s when it gets real.” Simon Krieter, wearing a helmet and a high-vis jacket, looks over at the construction site where three heavy-duty vehicles are at work. One digger is tearing down the old factory hall at CLAAS headquarters in Harsewinkel, while two others are sorting the scrap, separating metal from concrete, and loading containers. It’s mid-morning in early July, and the demolition team has been on site since 8 a.m. Finishing time will not be until it gets dark at around 10 p.m. “They’ll get rid of quite a lot today,” says Simon Krieter, 35, head of the ongoing modernization project, as the now full containers are loaded onto two trucks. The 15,000-square-meter construction site – big enough for two soccer pitches – has visibly emptied. Another step in the “SynPro 2020” project is completed. “Until a few days ago, we were planning largely on the basis of pilot projects and software,” says Krieter. “Now it’s happening for real.”
Does he feel a bit uncomfortable, now that diggers are tearing down this venerable building, in which combine harvesters were produced for almost 70 years and several generations of CLAAS employees worked? “No, not really,” says Krieter. “We spent almost four years carefully thinking through and planning everything that is happening.” The fact that it is now starting, that the diggers have made it real, “this is the beginning of the critical phase that we as a team have been eagerly anticipating.” He looks over again at the construction vehicles. One is demolishing, while the two others are sorting with a level of precision that almost has a meditative quality. “This is a demanding project,” says the mechanical engineering graduate who majored in production technology. But, if we’ll allow him to be casual for a moment, “above all it’s pretty exciting!”
This project is not about reducing costs. It’s an investment in the future, which will bring significant benefits for our customers and employees.”
Simon Krieter (left)
Two lines become one
“SynPro 2020” represents an extensive modernization of combine harvester production at CLAAS. The company is investing €44 million in this project, the core idea of which is to combine two previously separate assembly lines into one synchronous production system. “That’s possible,” explains Krieter, “because we are using more identical parts for the basic design of our models than we used to.” On the one hand, the latest generation of combine harvesters are almost all one of a kind, as they are fitted out and calibrated to meet each customer’s specific needs. On the other, the fundamental design of the models has been harmonized. This platform-based approach is the prerequisite for further expanding the company’s offering to its customers while still producing efficiently. So from the fall, only one assembly line will be required. However, this increase in efficiency is only one aspect of “SynPro 2020.” “The new combine harvester production system will ensure more quality and better jobs,” says Krieter. And he stresses one thing in particular: “This project is not about reducing costs. It’s an investment in the future, which will bring significant benefits for our customers and employees.”
For the project to work, the timing has to be right. “Delays are basically not an option,” says Krieter. As the company’s business follows a seasonal pattern, the production rhythm at CLAAS is helpful to the project: Production is in full swing from late fall to the harvest in the summer. Then comes the time when the machinery sold is in use and the focus turns to servicing. To match this rhythm, the team led by Krieter planned the project to make the best use of the quieter period, including the vacation closedown. “We developed a really simple month-by-month plan,” says Krieter. “Demolition in July, the steel structure and the roof in August, the building services in September, concreting in October, with moving in scheduled for November.” The team intentionally decided to have clearly defined steps. “They are easy to remember and make things transparent, which is good for communication.” If the plan works.
Krieter smiles: “Of course, there are risks with any construction project. It’s important to manage everything well.” This can be done using a data model that allows the team of engineers to walk through the project several times. “We’ve checked all the processes digitally,” says Krieter. Eventualities were anticipated and measures developed. That was the theory. Now the practical phase begins. “Right now we’re ...” – the project manager glances at his watch – “... four days ahead of schedule.” He nods contentedly, giving the air of a soccer coach whose team has just secured an important away victory.
Like open-heart surgery
Demolishing an old production hall and building a new one is basically nothing unusual for a company. What is unique about “SynPro 2020”? Björn Evers invites me onto the roof. The head of works planning leads the way, and our destination offers a new perspective of the construction site. From up here, the five big diggers look smaller but no less powerful. One thing is apparent from this vantage point: the construction site is at the heart of the production area, surrounded by sections of the halls that have already been modernized. If one imagines the CLAAS plant in Harsewinkel as a human body, then the demolition and replacement of the old hall, which was built in 1952 and 1958, is akin to open-heart surgery. And that is not without risks. “We need to build the new part so that it fits straight onto the existing halls – so that it is aligned in the truest sense of the word,” explains Evers. The construction engineer has been in the company’s works planning department since 2008. The plans for “SynPro 2020” have existed for many years, he reveals. “But four years ago, there was a key moment when I realized things would get underway soon,” he says. Helmut Claas – who passed away in early 2021, the son of the company founder August Claas – came into the production area, sat down and observed what was happening for about an hour: silently, with goodwill and an expert’s eye. He noticed that the production of the large combine harvesters always got stuck at the same point. At 4.20 meters, the height of the old hall was so low in many places that the engines could not be assembled onto the machines. This meant that production backed up, with some fitters having to wait, while others were under a lot of stress. “Helmut Claas recognized that these challenges required a new solution,” remembers Evers. Shortly afterwards, the first feasibility study for the project was presented. And it all started.
Helmut Claas recognized that a new solution was required.”
Björn Evers
Taking our people with us
We descend from the roof and head to the production area. That is where, from November 2021, combine harvesters will be manufactured on the new, combined assembly line in a hall, that at 14 meters, is more than three times as high as its predecessor. Sebastian Griestop takes a moment to get his bearings, then says: “My old desk was right here; my computer sat there.” The 31-year-old is team spokesman. He and his 13 colleagues work on module assembly for the LEXION combine harvester. “It feels pretty strange that our workplace has disappeared,” he says. The good news is they will soon have a new one: “roughly over there.” The last few months in the old building were challenging. On the one hand, combine harvester production was in full swing. Orders for the LEXION and TUCANO series were healthy, and the team did not want to keep customers waiting because of the redevelopment. On the other, Griestop and the other team spokespersons were simultaneously planning the transformation: The staff had to carefully label and pack up their tools and equipment just like we were relocating. “Our goal was to take our people with us in this process. That means openly communicating what the idea behind the project is and what the benefits for each one of us will be when we start again in November.” What will change? “Our work will flow better. The pace will increase,” he says. “And because we’ll have more space, it will be much easier to get hold of the right tool and material.”
Our work will flow better. The pace will increase.”
Sebastian Griestop
Picking at the supermarket
From November, procurement will happen at the supermarket – but not the one down the block. In the new intralogistics picking area. Julia Böhnke is department head. The 38-year-old industrial engineer has been with CLAAS for more than two years. Her team, which numbers 150 in the peak season, is tasked with ensuring the flow of material from receipt to production. In the right quantity and at the right time – ideally just when needed. A lack of material causes delays, while deliveries that are too early block space. “That’s why picking is always an important topic,” says Böhnke, “especially as the machines are getting more complex. Our customers’ wishes are becoming increasingly specific, which means the range of different object numbers is growing, despite limited space in the production area.” Converting combine harvester production to a single line and building a new hall are perfect opportunities to realign intralogistics. And that is where the supermarket comes in – a central location that stores the material to be picked, thus saving space at the production line. Böhnke describes how it will work: “Employees go through the alleys of material with our newly designed picking carts, with containers of material to their left and right. A digital cockpit enables the system to show them which parts from which box they need to put into the cart for that particular machine order.” This will prevent errors and mean no more paperwork for intralogistics. The supermarket will be installed exactly where the diggers are currently at work. “So we’re standing right in the middle of the production area. Intralogistics and manufacturing are converging, which makes sense because it keeps distances short,” says Böhnke. A test run has already taken place, with intralogistics operating a pilot supermarket for twelve months in the final assembly area. The experiences were positive, the technology worked, and initial learning effects were analyzed. “Using the knowledge we’ve gained, we will continue like this in the fall – the only difference being that significantly more parts will be picked at the new supermarket.”
Intralogistics and manufacturing are converging – which makes sense because it keeps distances short.”
Julia Böhnke
Variance thanks to modularization
A supermarket in the middle of the production area – it sounds unusual, but makes absolute sense to Bernd Schapmann and Bernd Schicketanz. “Manufacturing the new generation of combine harvesters took our conventional production system to its limits,” says Schapmann. “This comprehensive modernization project comes at exactly the right time.” He and Schicketanz have been with the company for many years. As heads of assembly, they have each been responsible for one of the two lines up to now. Their new task is to convert the processes to enable production on a single line from November. The past and the future meet as we walk through the halls. “Over there,” says Schapmann, pointing toward the tireless diggers, “I had my very first office here at CLAAS.” Does he feel nostalgic? “Only for a moment,” he says, “but that’s quickly replaced by a huge sense of joy at what’s to come.” Part of the future is waiting at the test bay – a combine harvester from the new TRION series, an all-arounder with the potential to be a bestseller. “The TRION is a prime example of a machine that we can offer and produce for our customers according to their individual wishes,” says Schicketanz. Customers benefit from the high variance, and the platform approach allows CLAAS to make its products efficiently. “That’s a win-win situation – for our customers and us as manufacturers. We will reap the benefits of this from November, once we start assembly on a single line.”
The TRION is a prime example of a machine that we can offer and produce for our customers according to their individual wishes.”
Bernd Schicketanz
Manufacturing the new generation of combine harvesters took our conventional production system to its limits.”
Bernd Schapmann
An unforgettable year
Back on the roof with Björn Evers, head of works planning. It is early evening and the demolition work is progressing. The project will maintain its four-day buffer. “That’s good,” says Evers, “but this year has taught me to be cautious with predictions.” The third wave of the coronavirus pandemic, the resulting shortage of material, as well as enormous amounts of snow in February, and then the storms in the summer. “We had plenty of challenges to overcome,” says Evers. He is already certain that this year will be long remembered in the history of the company. Down below, meanwhile, the production hall is emptying, the staff are finishing for the day; the summer holidays are beginning. This year, many employees will be on vacation longer than usual. Those who have accumulated lots of overtime can take these hours off while production is paused. That does not apply to works planner Björn Evers and project manager Simon Krieter. They are in charge of the processes and come to the construction site almost every day – and if not, they follow the progress via a webcam. Combine harvester production is scheduled to restart on November 29. Krieter describes the scenario: “Our colleagues will return and set up their workstations, intralogistics will open the supermarket, and assembly will gradually begin on the new line.” Then it will be his turn for vacation, right? “No, ‘SynPro 2020’ doesn’t end when the hall has been built, but when the hall is alive with activity, and operations are running smoothly.” That does not seem to bother him though. “You only manage such an extensive project once in a lifetime. And I’m enjoying it.”
Simon Krieter